Checking Out the Benefits of a Chemical Defoamer in Production and Production
The assimilation of chemical defoamers in production and production procedures uses a tactical benefit by addressing among the consistent challenges in commercial operations: foam control. Chemical Defoamer. Recognizing the nuances of different kinds of defoamers and their particular applications can disclose their significant influence on functional effectiveness and item quality. As producers make every effort to optimize procedures and boost customer fulfillment, the role of chemical defoamers ends up being significantly vital. Yet, the concern continues to be: how do these compounds fundamentally change the landscape of manufacturing efficiency and cost-effectiveness?
Value of Foam Control
While the presence of foam in producing procedures can occasionally seem safe, efficient foam control is crucial for enhancing operational effectiveness and item top quality. Foam can disrupt various stages of manufacturing, causing inefficiencies that might prolong and increase costs processing times. In markets such as food and beverage, pharmaceuticals, and chemicals, unrestrained foam can obstruct devices, interrupt automated systems, and ultimately cause product incongruities.

Executing efficient foam control methods not just boosts productivity but also supports governing conformity in sectors where foam can lead to ecological worries. By making use of chemical defoamers, manufacturers can reduce these difficulties, making sure smoother procedures and higher-quality final product. Ultimately, prioritizing foam control is an important element of manufacturing that can produce considerable benefits in terms of efficiency, product, and safety dependability.
Types of Chemical Defoamers
What types of chemical defoamers are readily available for producing processes, and how do they differ in application? Chemical defoamers can be categorized into three primary types: silicone-based, organic, and not natural defoamers. - Chemical Defoamer

Organic defoamers, normally derived from natural oils or fats, are effective in a series of applications, consisting of food and drink manufacturing. They are frequently liked for their reduced poisoning and environmental impact, making sure conformity with sector regulations.

Each kind of defoamer offers unique purposes based on the chemical make-up and the particular requirements of the production process, permitting makers to choose one of the most suitable alternative for their particular demands.
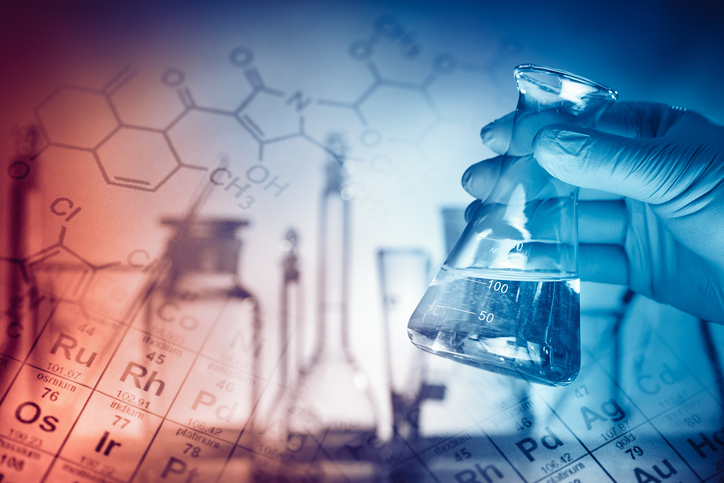
Advantages in Manufacturing Performance
Chemical defoamers play an important duty in improving making efficiency by properly controlling foam generation throughout numerous processes. Foam can prevent production rates, interfere with tools operation, and result in pricey downtime. By incorporating chemical defoamers, makers can mitigate these problems, making certain smoother workflow and boosted total efficiency.
Making use of chemical defoamers aids optimize the operational efficiency of tools such as mixers, pumps, and reactors. With decreased foam, these equipments can run at their intended capability, decreasing the threat of overflow and allowing constant handling. This results in better source utilization and higher throughput.
Furthermore, chemical defoamers assist in faster handling times by lowering the moment needed for foam elimination. This velocity can significantly influence manufacturing timetables, permitting manufacturers to meet customer demand better. Furthermore, using defoamers adds to decrease power intake, as equipment runs extra successfully with lowered foam disturbance.
Influence On Item Top Quality
Foam control is not just crucial for keeping performance in making procedures however likewise plays a considerable function in guaranteeing product quality. Excessive foam can present air right into formulas, causing variances in the final product. This can manifest as issues such as gaps, unequal structures, or substandard finishes, which threaten the desired high quality and performance of the product.
In addition, foam can prevent the homogeneity of blends, resulting in irregular distribution of active components. In markets such click here now as finishings, cosmetics, and food production, this can bring about variants in color, taste, and total effectiveness. By utilizing a chemical defoamer, suppliers can minimize these threats, ensuring that items satisfy stringent top quality specs.
Additionally, regulating foam can enhance the security of suspensions and solutions, which is important for guaranteeing shelf-life and customer fulfillment. With improved item consistency and lowered problems, manufacturers can accomplish higher requirements of quality guarantee, eventually causing enhanced consumer count on and brand name loyalty.
Cost-Effectiveness and ROI
Reliable foam find out control not only boosts item quality however also adds significantly to the general cost-effectiveness of making processes. Using chemical defoamers minimizes foam-related problems, which can or else result in manufacturing delays, devices breakdowns, and increased energy intake. By decreasing foam, suppliers can maximize their procedures, leading to greater throughput and performance.
Purchasing chemical defoamers can yield a considerable return on financial investment (ROI) The initial costs related to these additives are usually offset by the financial savings understood from decreased downtime and boosted product yield. Boosted item quality can reduce waste and remodel expenses, additionally strengthening economic efficiency.
In addition, effective foam control can result in decreased water and energy usage, adding to reduced functional expenses. This is especially crucial in sectors where source performance is extremely important. By incorporating chemical defoamers right into their procedures, suppliers can attain lasting financial savings while keeping affordable prices in the market.
Final Thought
In final thought, the combination of chemical defoamers in manufacturing and production procedures is essential for optimizing functional effectiveness and enhancing product high quality. Effective foam control adds to better equipment efficiency, decreased handling times, and decreased downtime, eventually causing considerable cost financial savings. In addition, constant product formulations foster consumer fulfillment and brand loyalty. The benefits used by chemical defoamers not only sustain governing compliance but additionally supply a competitive side in the production landscape.
The integration of chemical defoamers in production and production procedures provides a strategic benefit by resolving one of the consistent challenges in commercial operations: foam control.While the existence of foam in manufacturing procedures can sometimes appear harmless, efficient foam control is crucial for maximizing operational effectiveness and product high quality.Chemical defoamers play a crucial duty in enhancing check out this site producing effectiveness by properly managing foam generation throughout various processes.In addition, chemical defoamers assist in faster handling times by lowering the time needed for foam removal. Furthermore, the usage of defoamers adds to lower power intake, as machinery operates extra efficiently with decreased foam disturbance.
Comments on “Best Practices and Proven Ways for Using Chemical Defoamer in Different Processes”